In the world of Industry 4.0 technologies, digital twins stand out. They connect real objects and computer models. In India’s booming industry, they are key for better efficiency. Digital twins are not just copies. They are active models that keep up with real objects through data. This helps us make smart choices to improve product processes.
Simulation software and real data now lower the cost of building prototypes. By finding and solving issues early with virtual models, we save money and speed up product launches. Digital twins also use learning algorithms to predict maintenance needs. This cuts down on equipment downtime and saves money.
A McKinsey study shows 86% of industry experts see the value in digital twins, with a 44% adoption rate. This technology is used in many fields, from cars to planes. It helps uncover hidden wastefulness, cut extra work hours by up to 7%, and plan efficient production. This challenges old ways of making lots of products.
Key Takeaways
- Digital twins technology formulates a symbiotic relationship between the physical and the virtual, ushering in a new era of simulation software.
- These intelligent virtual modeling tools are a cornerstone of Industry 4.0, fueling smart manufacturing with real-time operational data.
- Virtual replicas are honing the predictive maintenance landscape, propelling industries toward minimized downtime and amplified productivity.
- The strategic use of digital twins enables businesses to optimize multiple processes, garnering improved efficiency and proactive maintenance solutions.
- With successful implementations across diverse sectors, digital twin technology proves to be a versatile ally in India’s industrial growth story.
Understanding Digital Twins Technology
Digital twin development is changing industries, offering deep insights and control. With a virtual representation of real things, they help in making smart decisions. They are key for analyzing data and maintaining equipment well.
Digital twins have grown with Industry 4.0, leading to breakthroughs in how we make things. They use live data from real objects. This gives us ongoing insights and helps predict future issues.
For example, a car simulation offers a practice setup without using a real car. But, a car’s digital twin connects with the actual vehicle. It gets updates and analyzes data to maintain the car better.
The design of a digital twin includes many parts that work together. It has sensors to gather data and advanced analytics to understand this data. This ensures they reflect the real object accurately and in real time.
The market for digital twins will grow a lot, expecting to hit $73.5 billion by 2027. This shows they are becoming important in many industries, from making things to health care.
For example, Anheuser-Busch InBev uses digital twins to make its brewing better and save money. Emirates Team New Zealand uses them to design faster boats.
Digital twins are growing with the help of generative AI. This makes their predictions better. Starting with smart planning, they move through detailed design to careful creation.
Digital twins are changing how we work, blending real-time data with deep analysis. They help in not just watching systems but in managing them before issues happen.
IoT Integration with Digital Twins
The mix of IoT and digital twins is changing how businesses work. These technologies help companies work better and adapt faster. They allow for real-time system monitoring and better management of industrial assets.
Connected devices are key to this change. They gather important data from many places. This data helps make digital twins match their real-life partners. This match lets businesses test out different futures with better accuracy.
Connecting Physical and Virtual Worlds
With IoT and digital twins, the physical and virtual worlds connect better. This lets companies test their systems and assets in real-time. It opens up new ways to develop products and solve problems.
Role of IoT Sensors in Data Collection
IoT sensors are crucial for collecting different types of information. They keep digital twins updated to match their real-world counterparts. This helps companies make smart decisions quickly.
Enhancing Operational Efficiency with IoT and Digital Twins
IoT and digital twins make operations more efficient in many industries. They help avoid machine downtime and offer better patient care. This is because the data they collect is so precise.
Industry | Benefit | Example of IoT Data Usage |
---|---|---|
Manufacturing | Reduced downtime through predictive maintenance | Equipment performance monitoring |
Oil and Gas | Optimized maintenance planning | Real-time monitoring of equipment |
Retail | Enhanced shopping experience | Analysis of consumer behavior |
Healthcare | Improved treatment decisions | Personalized patient modeling |
Sustainable Power | Increased network stability and performance | Optimization of energy output |
IoT and digital twins offer real-time monitoring and insights. They are practical tools that are changing industries. As companies keep using these technologies, their abilities will grow even more.
This makes the digital and physical worlds greatly benefit from each other.
Applications of Digital Twins in Various Sectors
Industries are always looking to get better and use new methods. Digital twins have become key in this quest. They help in many areas like making industries better, flying safer, and creating smarter cities. They also make a big difference in healthcare. Let’s see how these tools change different fields by making them work better and improving quality.
Read more: Smart medical devices | Ultimate Guide to Smart medical devices 2025
Read more: Artificial intelligence : What it is and why it matters in 2025
Read more: Metaverse Real Estate: Buying Virtual Land in the Digital World
Manufacturing: From Design to Predictive Maintenance
Digital twins make it easier to go from designing something to actually making it. They help keep factories running smoothly. This means less time fixing things and more time making them. Factories use digital twins to make their processes better, design better products, and fix problems before they happen. This cuts costs and increases how much they can make.
Healthcare: Personalized Medicine and Patient Care
The healthcare field gets a lot of help from digital twins. They work with IoT to change how we look after patients. This tech lets doctors create care plans just for you. It also helps predict health issues before they happen. This way, doctors can offer care that’s ahead of the game, not just reacting to problems.
Aerospace and Defense: Simulation for Safety and Efficiency
Using digital twins in aerospace keeps flights and defense systems safe and efficient. These simulations test different situations to see what might happen. This helps solve problems before they start. It makes sure that airplanes and defense systems are very safe and work really well, even under a lot of pressure.
Smart Cities: Urban Planning and Infrastructure Management
Smart cities use digital twins for better planning and managing resources. They build virtual models of cities to see the future of traffic, save energy, and make life better for everyone. With smart choices based on data, they can solve city problems in smarter ways.
Case Studies: Successful Digital Twin Implementation
Digital twin technology has changed how different sectors operate and predict future needs. We will look at examples showing how well this technology works.
Siemens is a great example of digital twins in action. They’ve made manufacturing better by cutting down on errors and making production faster. Boeing uses digital twins for predictive maintenance, which helps keep planes flying more smoothly by knowing when they need fixing.
Other big names also benefit from digital twins. Rolls-Royce monitors engines in real time, doubling maintenance times and cutting carbon emissions. Mars has teamed up with Azure and AI to improve their manufacturing, reducing downtime and waste.
Company | Technology Used | Outcome |
---|---|---|
Siemens | Digital Twins | Enhanced manufacturing efficiencies, reduced defects |
Boeing | Predictive Maintenance | Optimized aircraft performance, reduced downtime |
Rolls-Royce | Engine Monitoring | Longer maintenance intervals, significant emission reductions |
Mars | Azure, AI | Improved machine uptime, reduced waste |
Digital twins are essential for the digital era. They help businesses like Siemens and Boeing shape their future. As tech improves, digital twins will play a bigger role in innovation.
Conclusion
Through our journey, we saw how digital twins push industrial automation ahead. They act like twins for physical systems. This tech sits at the heart of the industrial internet. It lets us make updates in real-time and improve how we manage industrial stuff.
Even though we’ve made big steps with digital twins, we found areas that need more work. Things like better rules for how we report data are important. This helps make sure we use the tech right. We also need to teach people to deal with complex challenges. Plus, keeping data safe is super important.
Governments and different groups need to work together. This is key for making tech that can deal with big and complex systems.
Using DT in real life, like making machines or dashboards, shows they really help. They make things work better and are good for our planet. By wasting less and making things the green way, we’re onto something great. DT are opening doors to a smarter, better future in industry.
External source Links:
FAQ
What is a Digital Twin?
A digital twin is a virtual model of a physical object, process, or system. It updates in real-time with data. This helps in analysis and decision-making to improve performance and operation.
How have DT evolved in Industry 4.0?
In Industry 4.0, DT have grown. They now use IoT, AI, and machine learning for better simulations. They’ve gone from simple models to smart systems that boost innovation and efficiency.
What makes up the architecture of a DT?
DT have key parts like monitoring systems, IoT, data analysis, and cyber-physical interfaces. These parts work together for an accurate and responsive virtual copy of something physical.
How do IoT and DT work together?
IoT provides the data digital twins need to stay accurate. This helps virtual models match their physical versions better. It leads to smarter decisions and a deeper understanding of the monitored item.
What is the role of sensors in DT?
Sensors gather important data like temperature and movement. This info goes to the digital twin. It’s essential for the twin to mimic the real-world condition and behavior accurately.
Get in Touch with SJ Articles
Read more: AI in Cybersecurity Master Guide 2024
Read more: BioPrinting explanation very simply! 2025
Read more: What exactly is multimodal AI?
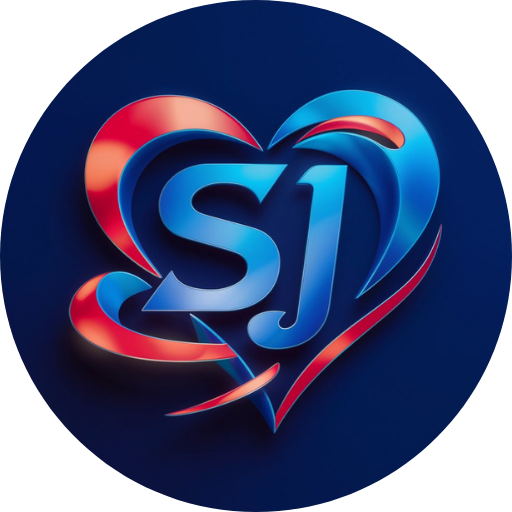